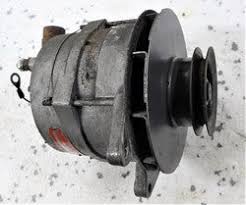
The aviation industry might make you think that aircraft alternators are made out of special materials, have been tested to impeccable standards and are manufactured on special production lines sprinkled with pixie dust. A normal engineer couldn’t hope to service one. The reality is that they are 1950’s or 1960’s American car (like Ford) alternators that wouldn’t stand up to the quality, power output or or rigours of a modern car alternator. Modern car alternators can produce a smooth output from 750 to 6000 rpm with little or no noise in the output because the tolerances and power electronics / frequency are far more advanced.
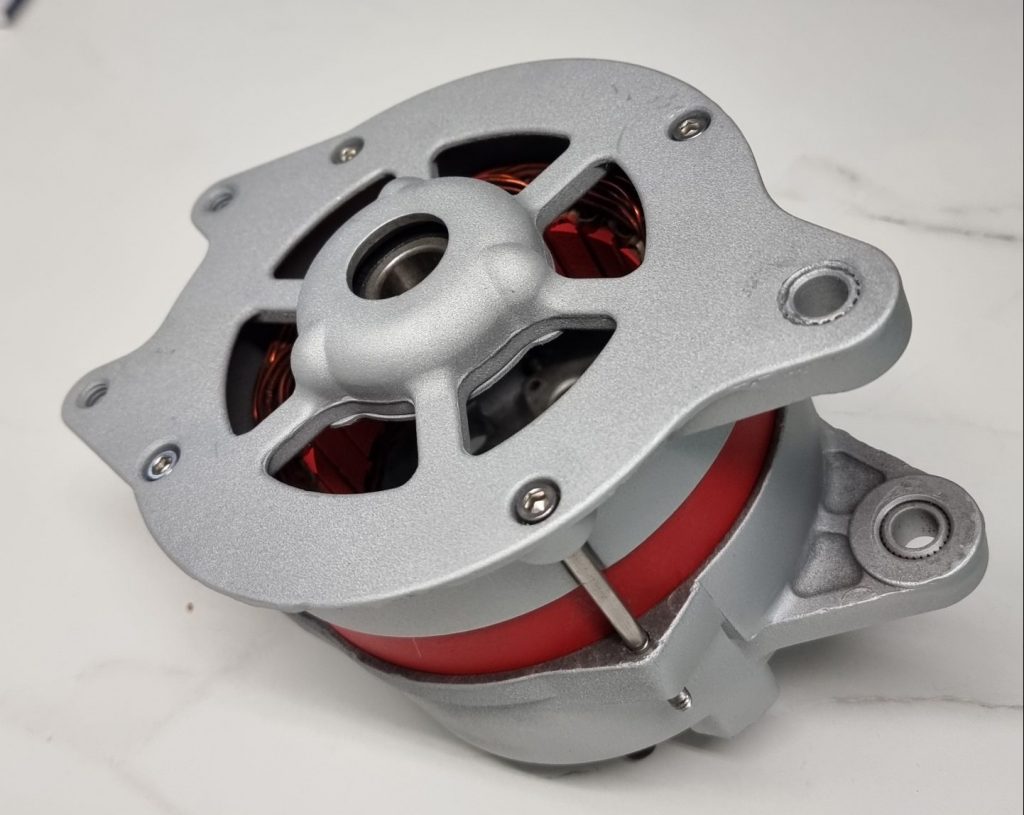
Basic Operation
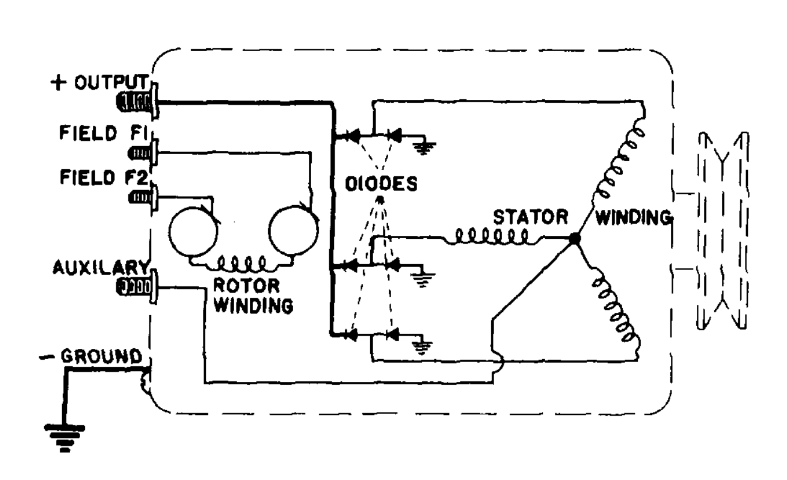
The principle of operation is simple, a rotating magnet induces an alternating current in a stator winding (hence the name alternator) that is then rectified and delivered to the battery.
The figure above shows the schematic layout. The stator would work with a single coil but by arranging 3 at 120 degrees (equally around the circle) the sine waves from each phase sums to a smooth output. In theory it shouldn’t whine or produce large amounts of ripple or pulse. This 3-phase approach also doesn’t require a return path at the centre of all 3 connected coils because each phase works against the other two. The aux output (at the centre of the windings) isn’t required and can be left unconnected.
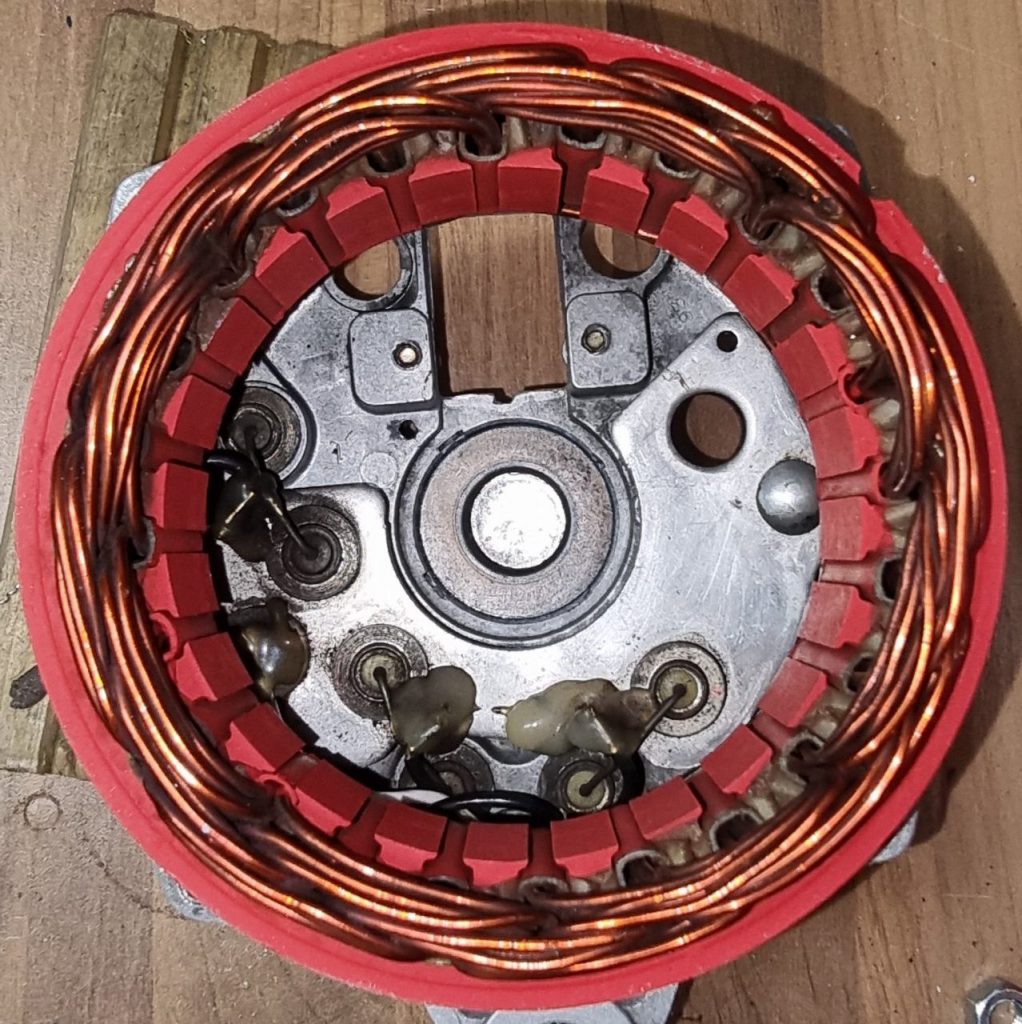
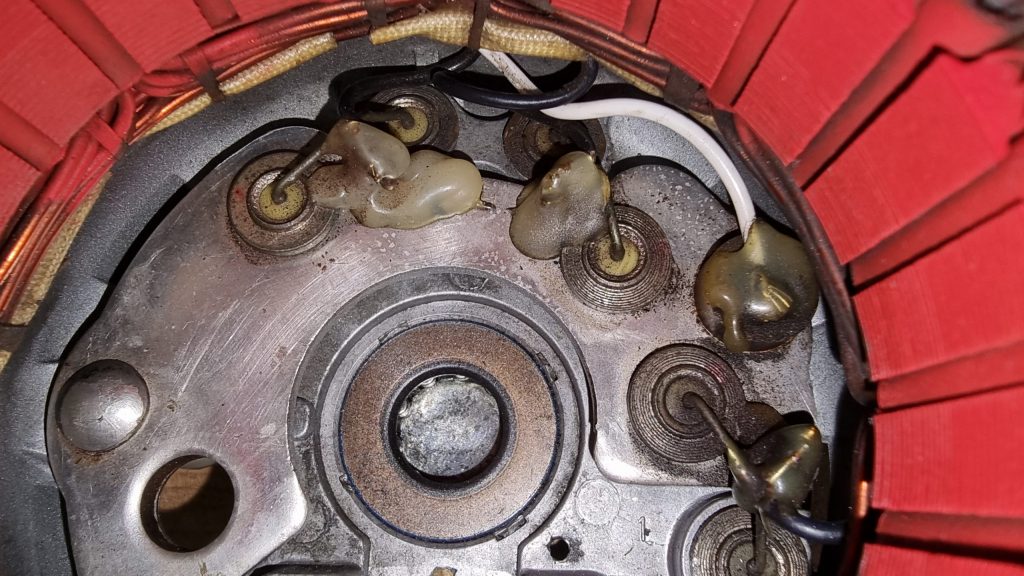
Regulation
We said that all we do is swing a magnet around in a coil to produce our output but obviously, there is more to it because that would overcharge the battery. If an alternator became detached from the battery, the output voltage may reach hundreds of volts.
Aircraft alternator regulators tend to be very simple on or off affairs and the electric regulators are in some cases mechanical. They are unreliable to the point that its typical to include an over voltage relay (OVR) which cuts off excitation completely if a preset output voltage is exceeded. For a 14V system this would typically be set to 16V. If the system reached 16V the relay will latch on turning the alternator off.
To regulate the alternator output we want a variable strength magnet in the rotor instead of a permanent magnet. In an alternator the rotor is an electromagnet and when the battery is low the strength of this magnet is high and when the battery is fully charged the magnet is its weakest and its the job of the regulator to control this. In a car this will be built into the alternator and it will use fast modulation of the rotor current in a closed control loop to produce an output that is always spot on. In an aircraft regulators tend to be separate units like they used to be in cars. In cars they stopped doing that because regulation control is poor, being affected by voltage drops, stray magnetic fields and radio interference as well as emitting radio interference all over the place. What normally happens when there is parasitic resistance is that the voltage will fluctuate, often oscillating, but even under the best situation its poor.
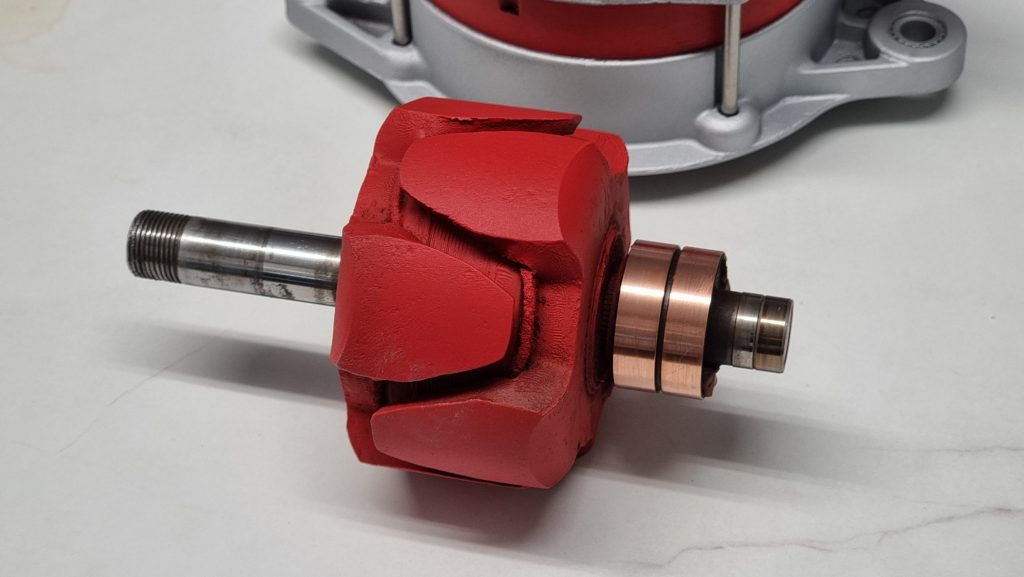
An electromagnet is just a winding, and winding around an iron core concentrates the field. As such, the rotor is a single winding around an iron former. The two interlocking sets of fingers are opposing poles (each end) of the electromagnet which means that the rotor actually has alternating N-S-N-S… arrangement. As we can see in the picture, one finger is part of one end and the next finger is part of the other end. Just like the stator where there are multiple windings, there are multiple poles rotating in the stator which improves output power.
The problem of how to connect the windings is solved using slip rings where graphite brushes are pressed against the rings by springs to maintain contact. The graphite has good conduction, is hard wearing and also lubricating.

The external regulator is a sealed unit that essentially varies the current flowing through the rotor from terminal F to ground via the output transistor T3. If T3 is fully on, then F would be driven to ground providing full current, typically 2 – 4 Amps.
The heart of the regulator is a reference voltage. A zener diode has a fixed voltage drop across it which can be used to work out if our measured voltage is above or below a threshold.
When the system voltage connected to ‘I’ terminal reaches a value at which the Zener diode connected to the divider network conducts, current will flow from the ‘I’ terminal through Rl through Z1 causing Tl to conduct which diverts the base current of T2 flowing from ‘I’ terminal through R4 to ground, turning off T2 which turns off T3, de-energizing the rotor Winding. When the alternator output voltage falls to a value which permits Z1 to cease conduction, Tl will turn off which turns on T2 and T3, re-energizing the rotor winding. Filtering is provided by C1 which usually dries out and can’t be fixed.
This type of regulator is on or off but happens so quickly that the average current flowing through the rotor should be proportional to the charge current required and thus we can loosely refer to it as “regulating”.
Its fairly easy to bench test the regulator by using a variable bench supply, and a bulb in place of the field coil, if the voltage is below about 14 the bulb should be on and should go out as the voltage rises. You can vary the point slightly using a variable resistor (potentiometer) P1.
Self Preservation
Of course, the rotor windings are unlikely to always have perfect connection to the regulator due to the slip ring arrangement and because the rotor is a big inductor, the resulting field collapse when it becomes interrupted will induce large voltages which would rapidly result in the destruction of T3. To quench these spikes the designer has used a neon bulb L1. This is quite neat, a neon bulb will strike an arc at about 95V and will then clamp the voltage to about 60V. I would expect the bulb to have a hard time if the slip rings were dirty and I’m not sure how often they fail in practice.
In contrast a modern automotive alternator such as Bosch has solid state protection, diodes with larger breakdown breakdown voltages and much more robust transistors. This means regulator failure isn’t really a thing even if the output is shorted or reversed. The most common failure mode is bearing failure or salt water corrosion.
For aviation alternators regulator, wiring faults, poor earths, marginal batteries, diode and brush failure are all so common that if it were in a car it would fail every 50,000 miles or so – which is about what you’d expect from a 1950’s alternator.
Finally, although the output ought to be smooth because of the use of 3-phase the diodes do take some forward voltage to conduct so the current will suddenly kick-in when they become forward-biased, and this can caused a whine on the electrical system that may be heard on radios and amplifiers. So an output capacitor is typically fitted to the output terminal to ground usually around 2.2uF. These also dry out and should be replaced if a whine is heard and they can be doubled up to get 4.4uf if its still an issue. The suppressors supplied with Prestolite alternators are between 1 and 2.2uf but they have such a high ESR (effective series resistance) of 15+ Ohms that they might as well not have bothered.